What Is a Polymer?
Have you ever ridden a bicycle or even a motorcycle? An essential part of the bike is the chain, which drives the back wheel. Chains are widely used in machinery and even jewelry, such as a bracelet or necklace. All chains share in common a structure made of links. These links are repeated units with similar or identical structure joined in some way. Think of a long train with many similar cars.
Linked chains are also important in chemistry. These kinds of chains are called polymers. The word comes from the Greek, polu meaning 'many' and meros meaning 'share.' A polymer is a chain of repeated units, calledmonomers. The unit of most natural polymers is typically an 'organic molecule', containing carbon - the stuff you, me and all living things are made of.

1. Natural Polymers. Polymers found in nature, mostly in plants and animal sources,are called natural polymers. A few examples are:
a. Polysaccharides. Starch and cellulose are very common examples of polysaccharides. They are the polymers of glucose. Starch is a chief food reserve of plants while cellulose is chief structural material of plants.
b. Proteins. These are the polymers of α-amino acids. They are building blocks of animal cells. They constitute indispensable part of our food. Wool, natural silk, leather, etc., are proteins.
c. Nucleic Acids. These are the polymers of various nucleotides. RNA and DNA are common examples.
d. Natural Rubber. Substance obtained from latex is a polymer of 2-methyl buta-I, 3-diene (isoprene).
It may be noted that polymers like polysaccharides, nucleic acids, proteins, etc., which control various life processes in plants and animals are also called biopolymers.
2. Semi-Synthetic Polymers. These are mostly derived from naturally occurring polymers by carrying out chemical modifications. For example,
H2SO4
Cellulose + (CH3CO)2O → Cellulose diacetate
Acetic anhydride
Cellulose diacetate is used in making threads, films, glasses, etc.
3. Synthetic Polymers. The polymers which are prepared in the laboratory are referred to as synthetic polymers or man-made polymers. Some examples of the synthetic polymers are polyethylene, polystyrene, PTFE synthetic rubber, nylon, PVC, bakelite, teflon, orion, etc.
The synthetic polymers can be further classified as these made up of monomers and comonomer units.
The polymers are also classified based on:
a) Structure
b) molecular forces
c) modes of polymerisation
Many polymeric materials having chain-like structures similar to polyethylene are known. Polymers formed by a straightforward linking together of monomer units, with no loss or gain of material, are calledaddition polymers or chain-growth polymers. A listing of some important addition polymers and their monomer precursors is presented in the following table.
Name(s)
|
Formula
|
Monomer
|
Properties
|
Uses
|
---|---|---|---|---|
Polyethylene low density (LDPE) | –(CH2-CH2)n– | ethylene CH2=CH2 | soft, waxy solid | film wrap, plastic bags |
Polyethylene high density (HDPE) | –(CH2-CH2)n– | ethylene CH2=CH2 | rigid, translucent solid | electrical insulation bottles, toys |
Polypropylene (PP) different grades | –[CH2-CH(CH3)]n– | propylene CH2=CHCH3 | atactic: soft, elastic solid isotactic: hard, strong solid | similar to LDPE carpet, upholstery |
Poly(vinyl chloride) (PVC) | –(CH2-CHCl)n– | vinyl chloride CH2=CHCl | strong rigid solid | pipes, siding, flooring |
Poly(vinylidene chloride) (Saran A) | –(CH2-CCl2)n– | vinylidene chloride CH2=CCl2 | dense, high-melting solid | seat covers, films |
Polystyrene (PS) | –[CH2-CH(C6H5)]n– | styrene CH2=CHC6H5 | hard, rigid, clear solid soluble in organic solvents | toys, cabinets packaging (foamed) |
Polyacrylonitrile (PAN, Orlon, Acrilan) | –(CH2-CHCN)n– | acrylonitrile CH2=CHCN | high-melting solid soluble in organic solvents | rugs, blankets clothing |
Polytetrafluoroethylene (PTFE, Teflon) | –(CF2-CF2)n– | tetrafluoroethylene CF2=CF2 | resistant, smooth solid | non-stick surfaces electrical insulation |
Poly(methyl methacrylate) (PMMA, Lucite, Plexiglas) | –[CH2-C(CH3)CO2CH3]n– | methyl methacrylate CH2=C(CH3)CO2CH3 | hard, transparent solid | lighting covers, signs skylights |
Poly(vinyl acetate) (PVAc) | –(CH2-CHOCOCH3)n– | vinyl acetate CH2=CHOCOCH3 | soft, sticky solid | latex paints, adhesives |
cis-Polyisoprene natural rubber | –[CH2-CH=C(CH3)-CH2]n– | isoprene CH2=CH-C(CH3)=CH2 | soft, sticky solid | requires vulcanization for practical use |
Polychloroprene (cis + trans) (Neoprene) | –[CH2-CH=CCl-CH2]n– | chloroprene CH2=CH-CCl=CH2 | tough, rubbery solid | synthetic rubber oil resistant |
Synthesis of Addition Polymers
All the monomers from which addition polymers are made are alkenes or functionally substituted alkenes.
It is useful to distinguish four polymerization procedures fitting this general description.
• Radical Polymerization The initiator is a radical, and the propagating site of reactivity (*) is a carbon radical.
• Cationic Polymerization The initiator is an acid, and the propagating site of reactivity (*) is a carbocation.
• Anionic Polymerization The initiator is a nucleophile, and the propagating site of reactivity (*) is a carbanion.
• Coordination Catalytic Polymerization The initiator is a transition metal complex, and the propagating site of reactivity (*) is a terminal catalytic complex.

• Radical Polymerization The initiator is a radical, and the propagating site of reactivity (*) is a carbon radical.
• Cationic Polymerization The initiator is an acid, and the propagating site of reactivity (*) is a carbocation.
• Anionic Polymerization The initiator is a nucleophile, and the propagating site of reactivity (*) is a carbanion.
• Coordination Catalytic Polymerization The initiator is a transition metal complex, and the propagating site of reactivity (*) is a terminal catalytic complex.
1. Radical Chain-Growth Polymerization
Virtually all of the monomers described above are subject to radical polymerization. Since this can be initiated by traces of oxygen or other minor impurities, pure samples of these compounds are often "stabilized" by small amounts of radical inhibitors to avoid unwanted reaction. When radical polymerization is desired, it must be started by using a radical initiator, such as a peroxide or certain azo compounds. The formulas of some common initiators, and equations showing the formation of radical species from these initiators are presented below.
By using small amounts of initiators, a wide variety of monomers can be polymerized. One example of this radical polymerization is the conversion of styrene to polystyrene, shown in the following diagram. The first two equations illustrate the initiation process, and the last two equations are examples of chain propagation. Each monomer unit adds to the growing chain in a manner that generates the most stable radical. Since carbon radicals are stabilized by substituents of many kinds, the preference for head-to-tail regioselectivity in most addition polymerizations is understandable. Because radicals are tolerant of many functional groups and solvents (including water), radical polymerizations are widely used in the chemical industry.
Virtually all of the monomers described above are subject to radical polymerization. Since this can be initiated by traces of oxygen or other minor impurities, pure samples of these compounds are often "stabilized" by small amounts of radical inhibitors to avoid unwanted reaction. When radical polymerization is desired, it must be started by using a radical initiator, such as a peroxide or certain azo compounds. The formulas of some common initiators, and equations showing the formation of radical species from these initiators are presented below.
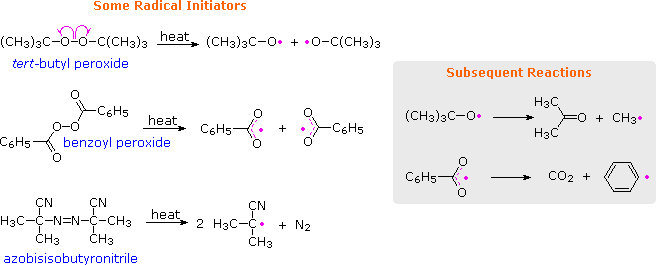
By using small amounts of initiators, a wide variety of monomers can be polymerized. One example of this radical polymerization is the conversion of styrene to polystyrene, shown in the following diagram. The first two equations illustrate the initiation process, and the last two equations are examples of chain propagation. Each monomer unit adds to the growing chain in a manner that generates the most stable radical. Since carbon radicals are stabilized by substituents of many kinds, the preference for head-to-tail regioselectivity in most addition polymerizations is understandable. Because radicals are tolerant of many functional groups and solvents (including water), radical polymerizations are widely used in the chemical industry.
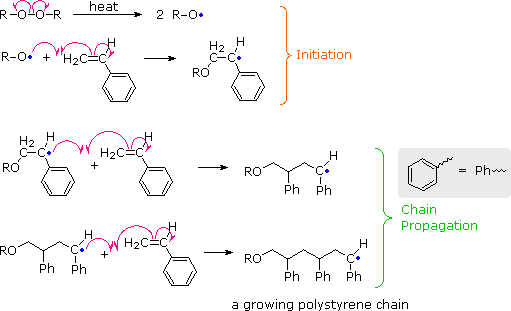
2. Cationic Chain-Growth Polymerization
Polymerization of isobutylene (2-methylpropene) by traces of strong acids is an example of cationic polymerization. The polyisobutylene product is a soft rubbery solid, Tg = _70º C, which is used for inner tubes. This process is similar to radical polymerization, as demonstrated by the following equations. Chain growth ceases when the terminal carbocation combines with a nucleophile or loses a proton, giving a terminal alkene (as shown here).
Monomers bearing cation stabilizing groups, such as alkyl, phenyl or vinyl can be polymerized by cationic processes. These are normally initiated at low temperature in methylene chloride solution. Strong acids, such as HClO4 , or Lewis acids containing traces of water (as shown above) serve as initiating reagents. At low temperatures, chain transfer reactions are rare in such polymerizations, so the resulting polymers are cleanly linear (unbranched).
Polymerization of isobutylene (2-methylpropene) by traces of strong acids is an example of cationic polymerization. The polyisobutylene product is a soft rubbery solid, Tg = _70º C, which is used for inner tubes. This process is similar to radical polymerization, as demonstrated by the following equations. Chain growth ceases when the terminal carbocation combines with a nucleophile or loses a proton, giving a terminal alkene (as shown here).
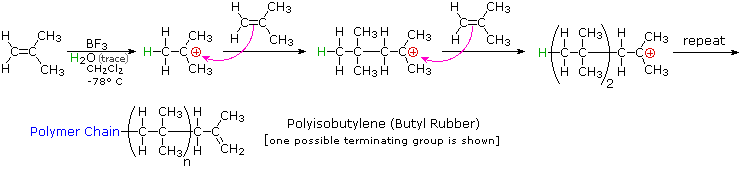
Monomers bearing cation stabilizing groups, such as alkyl, phenyl or vinyl can be polymerized by cationic processes. These are normally initiated at low temperature in methylene chloride solution. Strong acids, such as HClO4 , or Lewis acids containing traces of water (as shown above) serve as initiating reagents. At low temperatures, chain transfer reactions are rare in such polymerizations, so the resulting polymers are cleanly linear (unbranched).
3. Anionic Chain-Growth Polymerization
Treatment of a cold THF solution of styrene with 0.001 equivalents of n-butyllithium causes an immediate polymerization. This is an example of anionic polymerization, the course of which is described by the following equations. Chain growth may be terminated by water or carbon dioxide, and chain transfer seldom occurs. Only monomers having anion stabilizing substituents, such as phenyl, cyano or carbonyl are good substrates for this polymerization technique. Many of the resulting polymers are largely isotactic in configuration, and have high degrees of crystallinity.
Species that have been used to initiate anionic polymerization include alkali metals, alkali amides, alkyl lithiums and various electron sources. A practical application of anionic polymerization occurs in the use of superglue. This material is methyl 2-cyanoacrylate, CH2=C(CN)CO2CH3. When exposed to water, amines or other nucleophiles, a rapid polymerization of this monomer takes place.
Treatment of a cold THF solution of styrene with 0.001 equivalents of n-butyllithium causes an immediate polymerization. This is an example of anionic polymerization, the course of which is described by the following equations. Chain growth may be terminated by water or carbon dioxide, and chain transfer seldom occurs. Only monomers having anion stabilizing substituents, such as phenyl, cyano or carbonyl are good substrates for this polymerization technique. Many of the resulting polymers are largely isotactic in configuration, and have high degrees of crystallinity.
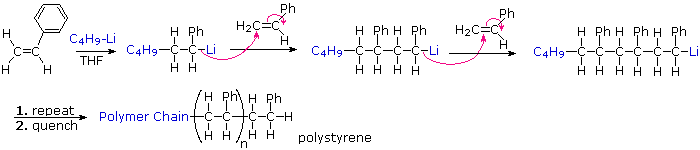
Species that have been used to initiate anionic polymerization include alkali metals, alkali amides, alkyl lithiums and various electron sources. A practical application of anionic polymerization occurs in the use of superglue. This material is methyl 2-cyanoacrylate, CH2=C(CN)CO2CH3. When exposed to water, amines or other nucleophiles, a rapid polymerization of this monomer takes place.
Copolymers
The synthesis of macromolecules composed of more than one monomeric repeating unit has been explored as a means of controlling the properties of the resulting material. In this respect, it is useful to distinguish several ways in which different monomeric units might be incorporated in a polymeric molecule. The following examples refer to a two component system, in which one monomer is designated A and the other B.
The synthesis of macromolecules composed of more than one monomeric repeating unit has been explored as a means of controlling the properties of the resulting material. In this respect, it is useful to distinguish several ways in which different monomeric units might be incorporated in a polymeric molecule. The following examples refer to a two component system, in which one monomer is designated A and the other B.
1. Addition Copolymerization
Most direct copolymerizations of equimolar mixtures of different monomers give statistical copolymers, or if one monomer is much more reactive a nearly homopolymer of that monomer. The copolymerization of styrene with methyl methacrylate, for example, proceeds differently depending on the mechanism. Radical polymerization gives a statistical copolymer. However, the product of cationic polymerization is largely polystyrene, and anionic polymerization favors formation of poly(methyl methacrylate). In cases where the relative reactivities are different, the copolymer composition can sometimes be controlled by continuous introduction of a biased mixture of monomers into the reaction.
Formation of alternating copolymers is favored when the monomers have different polar substituents (e.g. one electron withdrawing and the other electron donating), and both have similar reactivities toward radicals. For example, styrene and acrylonitrile copolymerize in a largely alternating fashion.
Most direct copolymerizations of equimolar mixtures of different monomers give statistical copolymers, or if one monomer is much more reactive a nearly homopolymer of that monomer. The copolymerization of styrene with methyl methacrylate, for example, proceeds differently depending on the mechanism. Radical polymerization gives a statistical copolymer. However, the product of cationic polymerization is largely polystyrene, and anionic polymerization favors formation of poly(methyl methacrylate). In cases where the relative reactivities are different, the copolymer composition can sometimes be controlled by continuous introduction of a biased mixture of monomers into the reaction.
Formation of alternating copolymers is favored when the monomers have different polar substituents (e.g. one electron withdrawing and the other electron donating), and both have similar reactivities toward radicals. For example, styrene and acrylonitrile copolymerize in a largely alternating fashion.
Formation of alternating copolymers is favored when the monomers have different polar substituents (e.g. one electron withdrawing and the other electron donating), and both have similar reactivities toward radicals. For example, styrene and acrylonitrile copolymerize in a largely alternating fashion.
Some Useful Copolymers
Monomer A
Monomer B
Copolymer
Uses
H2C=CHCl H2C=CCl2 Saran films & fibers
H2C=CHC6H5 H2C=C-CH=CH2 SBR
styrene butadiene rubber tires
H2C=CHCN H2C=C-CH=CH2 Nitrile Rubber adhesives
hoses
H2C=C(CH3)2 H2C=C-CH=CH2 Butyl Rubber inner tubes
F2C=CF(CF3) H2C=CHF Viton gaskets
Monomer A
|
Monomer B
|
Copolymer
|
Uses
|
---|---|---|---|
H2C=CHCl | H2C=CCl2 | Saran | films & fibers |
H2C=CHC6H5 | H2C=C-CH=CH2 | SBR styrene butadiene rubber | tires |
H2C=CHCN | H2C=C-CH=CH2 | Nitrile Rubber | adhesives hoses |
H2C=C(CH3)2 | H2C=C-CH=CH2 | Butyl Rubber | inner tubes |
F2C=CF(CF3) | H2C=CHF | Viton | gaskets |
Condensation Polymers
A large number of important and useful polymeric materials are not formed by chain-growth processes involving reactive species such as radicals, but proceed instead by conventional functional group transformations of polyfunctional reactants. These polymerizations often (but not always) occur with loss of a small byproduct, such as water, and generally (but not always) combine two different components in an alternating structure. The polyester Dacron and the polyamide Nylon 66, shown here, are two examples of synthetic condensation polymers, also known as step-growth polymers. In contrast to chain-growth polymers, most of which grow by carbon-carbon bond formation, step-growth polymers generally grow by carbon-heteroatom bond formation (C-O & C-N in Dacron & Nylon respectively). Although polymers of this kind might be considered to be alternating copolymers, the repeating monomeric unit is usually defined as a combined moiety.
Examples of naturally occurring condensation polymers are cellulose, the polypeptide chains of proteins, and poly(β-hydroxybutyric acid), a polyester synthesized in large quantity by certain soil and water bacteria. Formulas for these will be displayed below by clicking on the diagram.
Examples of naturally occurring condensation polymers are cellulose, the polypeptide chains of proteins, and poly(β-hydroxybutyric acid), a polyester synthesized in large quantity by certain soil and water bacteria. Formulas for these will be displayed below by clicking on the diagram.
1. Characteristics of Condensation Polymers
Condensation polymers form more slowly than addition polymers, often requiring heat, and they are generally lower in molecular weight. The terminal functional groups on a chain remain active, so that groups of shorter chains combine into longer chains in the late stages of polymerization. The presence of polar functional groups on the chains often enhances chain-chain attractions, particularly if these involve hydrogen bonding, and thereby crystallinity and tensile strength. The following examples of condensation polymers are illustrative.
Note that for commercial synthesis the carboxylic acid components may actually be employed in the form of derivatives such as simple esters. Also, the polymerization reactions for Nylon 6 and Spandex do not proceed by elimination of water or other small molecules. Nevertheless, the polymer clearly forms by a step-growth process.
Note that for commercial synthesis the carboxylic acid components may actually be employed in the form of derivatives such as simple esters. Also, the polymerization reactions for Nylon 6 and Spandex do not proceed by elimination of water or other small molecules. Nevertheless, the polymer clearly forms by a step-growth process.
Some Condensation Polymers
Formula
|
Type
|
Components
| ||
---|---|---|---|---|
~[CO(CH2)4CO-OCH2CH2O]n~ | polyester | HO2C-(CH2)4-CO2H HO-CH2CH2-OH | ||
![]() | polyester Dacron Mylar | para HO2C-C6H4-CO2H HO-CH2CH2-OH | ||
![]() | polyester | meta HO2C-C6H4-CO2H HO-CH2CH2-OH | ||
![]() | polycarbonate Lexan | (HO-C6H4-)2C(CH3)2 (Bisphenol A) X2C=O (X = OCH3 or Cl) | ||
~[CO(CH2)4CO-NH(CH2)6NH]n~ | polyamide Nylon 66 | HO2C-(CH2)4-CO2H H2N-(CH2)6-NH2 | 45 | 265 |
~[CO(CH2)5NH]n~ | polyamide Nylon 6 Perlon | ![]() | ||
![]() | polyamide Kevlar | para HO2C-C6H4-CO2H para H2N-C6H4-NH2 | ||
![]() | polyamide Nomex | meta HO2C-C6H4-CO2H meta H2N-C6H4-NH2 | ||
![]() | polyurethane Spandex | HOCH2CH2OH![]() |
Biodegradable Polymers
Plastics derived from natural materials, such as cellulose, starch and hydroxycarboxylic acids are more easily decomposed when exposed to oxygen, water, soil organisms and sunlight than are most petroleum based polymers. The glycoside linkages in polysaccharides and the ester groups in polyesters represent points of attack by the enzymes of microorganisms that facilitate their decomposition. Such biodegradable materials can be composted, broken down and returned to the earth as useful nutrients.
The two natural polyesters that are finding increasing use as replacements for petroleum based plastics are polylactide (PLA) and polyhydroxyalkanoates (PHA), the latter most commonly as copolymers with polyhydroxybutyrate (PHB). Structures for the these polymers and their monomer precursors are shown below.
![]() | ![]() |
---|
cross linked polymers
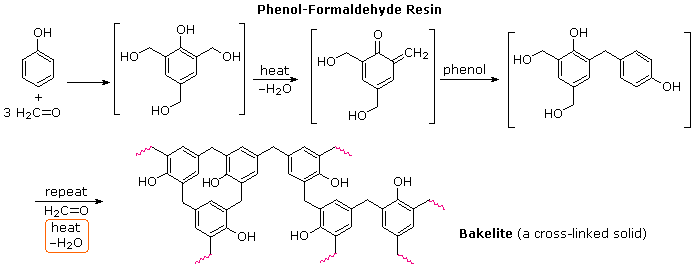
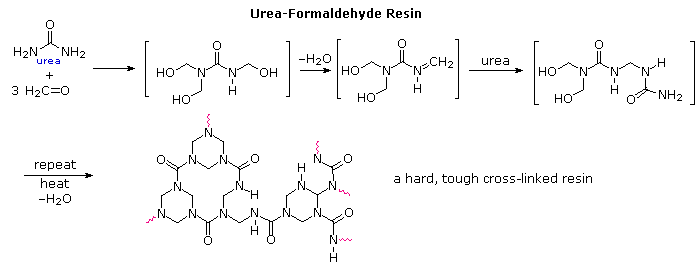
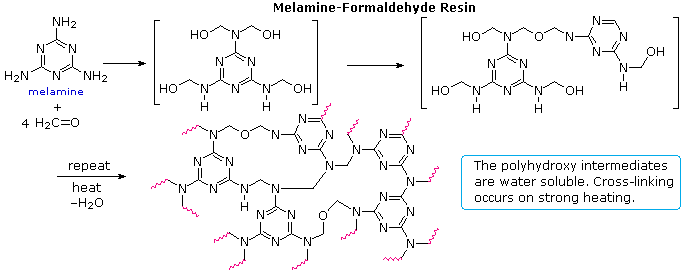
Nylon 66 is synthesised by polycondensation of hexamethylenediamine and adipic acid. Equivalent amounts of hexamethylenediamine and adipic acid are combined with water in a reactor.
n HOOC-(CH2)4-COOH + n H2N-(CH2)6-NH2 → [-OC-( CH2)4-CO-NH-(CH2)6-NH-]n + 2n H2O
toward polymerization through the formation of amide bonds from the acid and amine functions. Thus molten nylon 66 is formed.

Nylon 6
Nylon 6 is synthesized by ring-opening polymerization of caprolactam. Caprolactam has 6 carbons, hence 'Nylon 6'. When caprolactam is heated at about 533 K in an inert atmosphere of nitrogen for about 4-5 hours, the ring breaks and undergoespolymerization. Then the molten mass is passed through spinnerets to form fibres of Nylon 6.
During polymerization, the amide bond within each caprolactam molecule is broken, with the active groups on each side re-forming two new bonds as the monomer becomes part of the polymer backbone. Unlike nylon 6,6, in which the direction of the amide bond reverses at each bond, all nylon 6 amide bonds lie in the same direction (see figure: note the N to C orientation of each amide bond).
Polyethylene terephthalate (sometimes written poly(ethylene terephthalate), commonly abbreviated PET, PETE, or the obsolete PETP or PET-P, is the most common thermoplastic polymer resin of the polyester family and is used in fibers for clothing, containers for liquids and foods, thermoforming for manufacturing, and in combination with glass fiber for engineering resins.
It may also be referred to by the brand name Dacron; in Britain, Terylene;[4] or, in Russia and the former Soviet Union, Lavsan.

Natural Rubber

Structure of Natural Rubber
Back to Top
Natural rubber is a linear polymer of an unsaturated hydrocarbon called isoprene (2-methyl butadiene). There may be as many as 11,000 to 20,000 isoprene units in a polymer chain of natural rubber.

Hot Vulcanisation
Raw dry rubber is heated with sulphur (5%-8% based on the requirement), zinc oxide (a filler, 5%) and accelerator (0.5% -1%) at 400-440K for about half an hour. As the sulphur quantity increases, the rubber becomes tougher. 50% sulphur gives ebonite (vulcanite). An accelerator containing nitrogen, sulphur or both is used to increase the reaction rate and for vulcanisation to occur at room temperatures.

Comparison between raw natural rubber and vulcanised natural rubber
Back to TopRaw Natural Rubber | Vulcanized Natural Rubber |
---|---|
Soft and sticky | Comparatively hard and non-sticky |
Low tensile strength and not very strong | High tensile strength and very strong |
Low elasticity | High elasticity |
Can be used over a narrow range of temperature from 10 to 60 degrees centigrade | Can be used over a wide range of temperature from -40 to 100 degrees centigrade |
Low abrasion resistance | High abrasion resistance |
Absorbs a large amount of water | Absorbs a small amount of water |
Soluble in solvents like ether, carbon disu p hide, carbon tetrachlo ride, petrol and turpentine | Insoluble in all the usual solvents |
synthetic rubber
To meet human needs, scientists have started preparing synthetic rubbers. Besides having similar properties as natural rubbers they are tougher, more flexible and more durable than natural rubber. They are capable of getting stretched to twice its length. Though, it reverts to its original shape and size once the external stretching force is released.
Synthetic rubbers have been made by the polymerisation of dienes other than isoprene. The polymerisation is carried out in the presence of Zeigher-Natta catalyst. For example, Polymerisation of 1, 3-butadiene
Preparation of synthetic rubbers
1. Neoprene or polychloro prene is formed by the free radical polymerisation of chloroprene.
It has superior resistance to vegetable and mineral oils. It is used for manufacturing of conveyer belts, gaskets and hoses.
2. Buna-N: you have previously studied about Buna-S. Buna-N is obtained by the copolymerization of 1, 3-butadiene and Acrylonitrile in the presence of a peroxide catalyst.
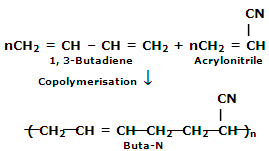
It is resistant to the reaction of petrol, lubricating oil and organic solvents. It is utilized in making oil seals, tank lining etc.
Thank you,It has been helpful
ReplyDeleteVery informative post! There is a lot of information here that can help any business get started with a successful social networking campaign!
ReplyDeleteNon-Asbestos Gaskets